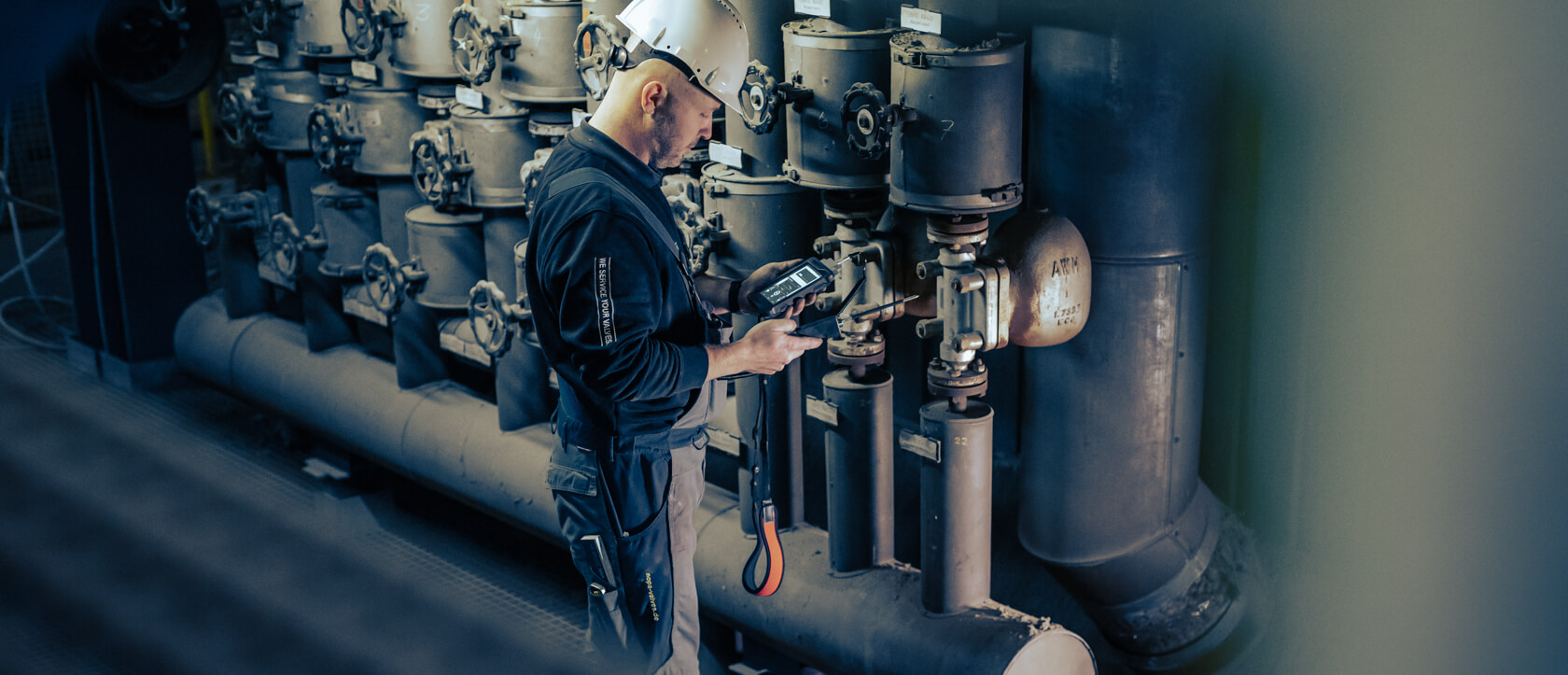
regular maintenance prevents damage
Regular maintenance prevents damage
Steam trap service
Defective steam traps hover over your business like a sword of damocles. They can cause enormous economic damage every year and put your operations in checkmate within a very short time. In addition to the loss of steam due to leakage, this can also result in damage to the entire system or individual plant components. Even if only individual steam traps are affected, regular maintenance is worthwhile to prevent further damage and enormous economic losses.
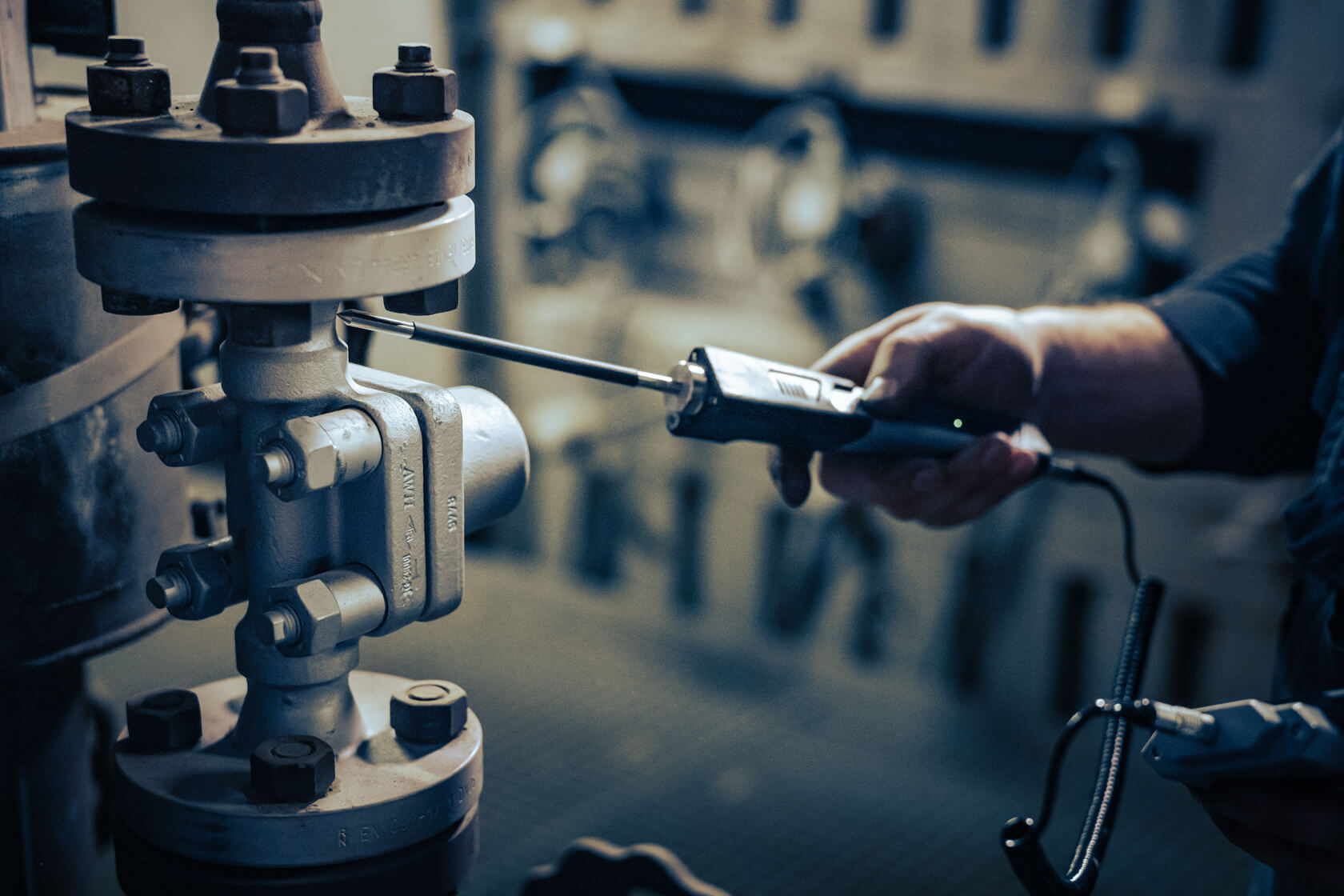
Calculation example: this is the effect
the maintenance of the steam traps
- Defective steam traps: 15 pieces
- Steam loss per steam trap: 4 kg/h
- Operating hours per year: 9,500 hours
- Steam losses per year: 570 t
- Cost of one ton of steam: 25 euros
- Total loss per year: 14,250 euro
- Co2 savings per year: 91,200 kg
Imagine if there were 15 defective steam traps in your plant. Do you have any idea of the losses they would cause you every year – not to mention the dangers to your employees and equipment? Our sample calculation shows the economic potential of steam trap maintenance.
In this example, regular steam trap maintenance could save you 14,250 euros a year.
Damage due to defective steam traps
the savings calculator
How much can your company save annually on steam trap maintenance? Use our pre-filled experience values or enter your own calculation factors. Based on the information you provide, the calculator will determine what defective steam traps could cost your company per year.
Calculate your annual savings with our calculator. Values already filled in are our empirical values. However, you can change them at any time.
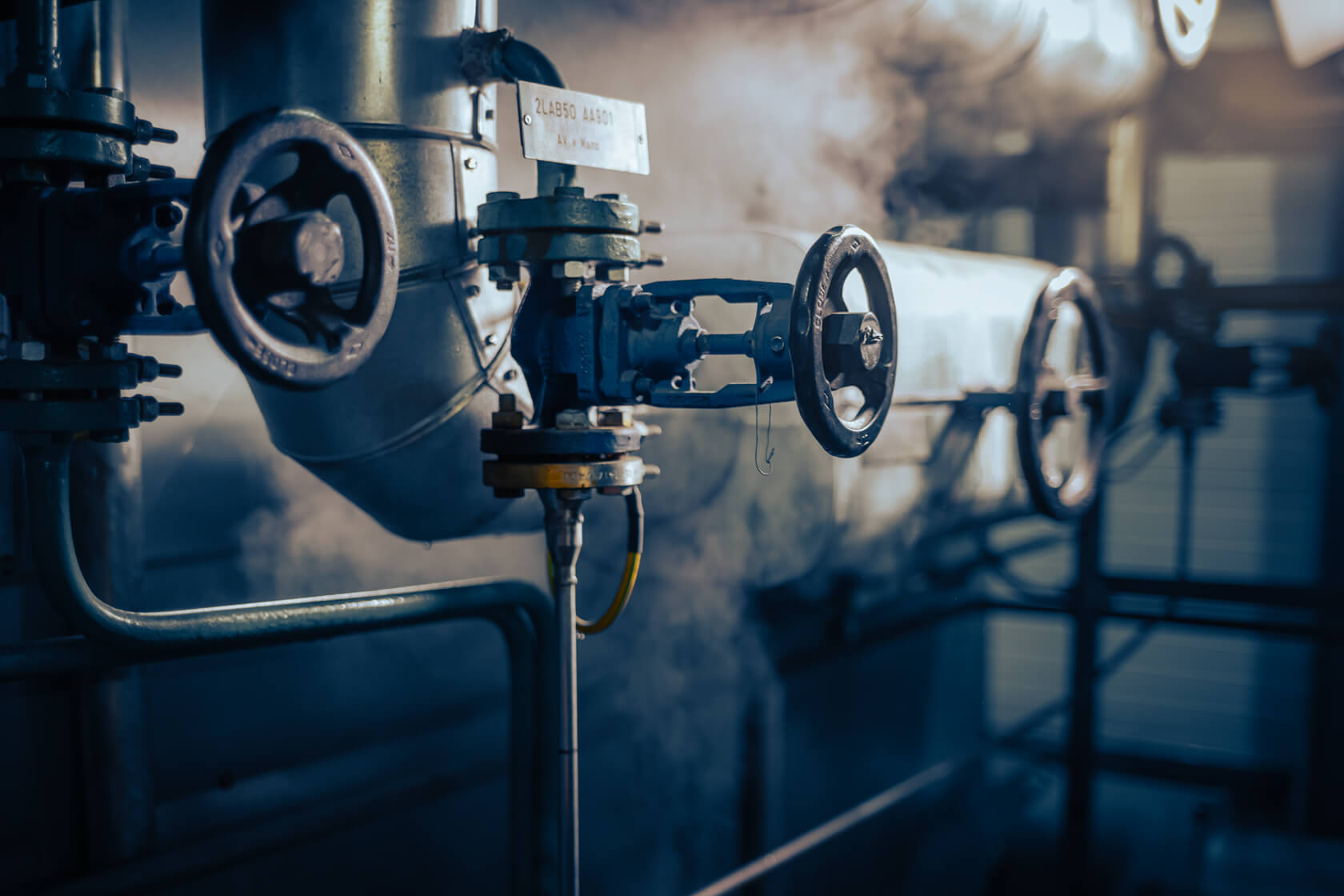
Causes of defective
Steam traps
A variety of factors can contribute to a steam trap malfunctioning:
- Condensate buildup occurs in clogged steam traps. This results in undesirable subcooling, backflow into areas not approved for it, and the risk of freezing or water hammer.
- Fouling or deposits in the steam trap result in loss of capacity or even damage to the system.
- If a steam trap is blocked, it reduces the heating capacity of the consumer. Water hammering caused by this can cause significant damage to the steam and condensate system.
- If steam is lost due to leakage, this water loss must be compensated. An appropriate amount of fresh water must be supplied to the system. In addition, the pressure in the condensate networks increases at other drainage points, which can lead to drainage problems.
All these factors contribute to reducing the profitability of your production. With regular steam trap maintenance, you can save huge costs each year, optimizing your bottom.
Steam trap maintenance
Without downtime during operation
The regular maintenance of steam traps by the NOPA service team is characterized by these special features:

Steam trap maintenance without downtime and installation
Thanks to modern ultrasonic diagnostics, our service team is able to check your steam traps while steam systems are in operation. This means that it is not necessary to interrupt the operating process for steam trap maintenance. Only if an impaired functionality is detected, a short shutdown is necessary.
Long-term inspection
Based on the detailed test records that our service technicians prepare for each maintenance, we can carry out comparative measurements at fixed intervals. If there is any indication of a malfunction, steam traps can be replaced or repaired at an early stage before they can cause major damage.
Lower failure rates
Based on experience, failure rates of 15 to 25 percent can be expected if a system is not regularly inspected or serviced. Our service technicians prevent failure by performing regular steam trap maintenance. With a minimum annual maintenance interval, the failure rate can be reduced to as low as 5 percent. Plant availability increases significantly.
Lower susceptibility to failure with special steam traps
We recommend that our customers use special steam traps that are less susceptible to malfunctions. We achieve this by using corrosion-resistant thermobimetals, a more robust design and automatic venting. We will be happy to assist you in choosing the right product.
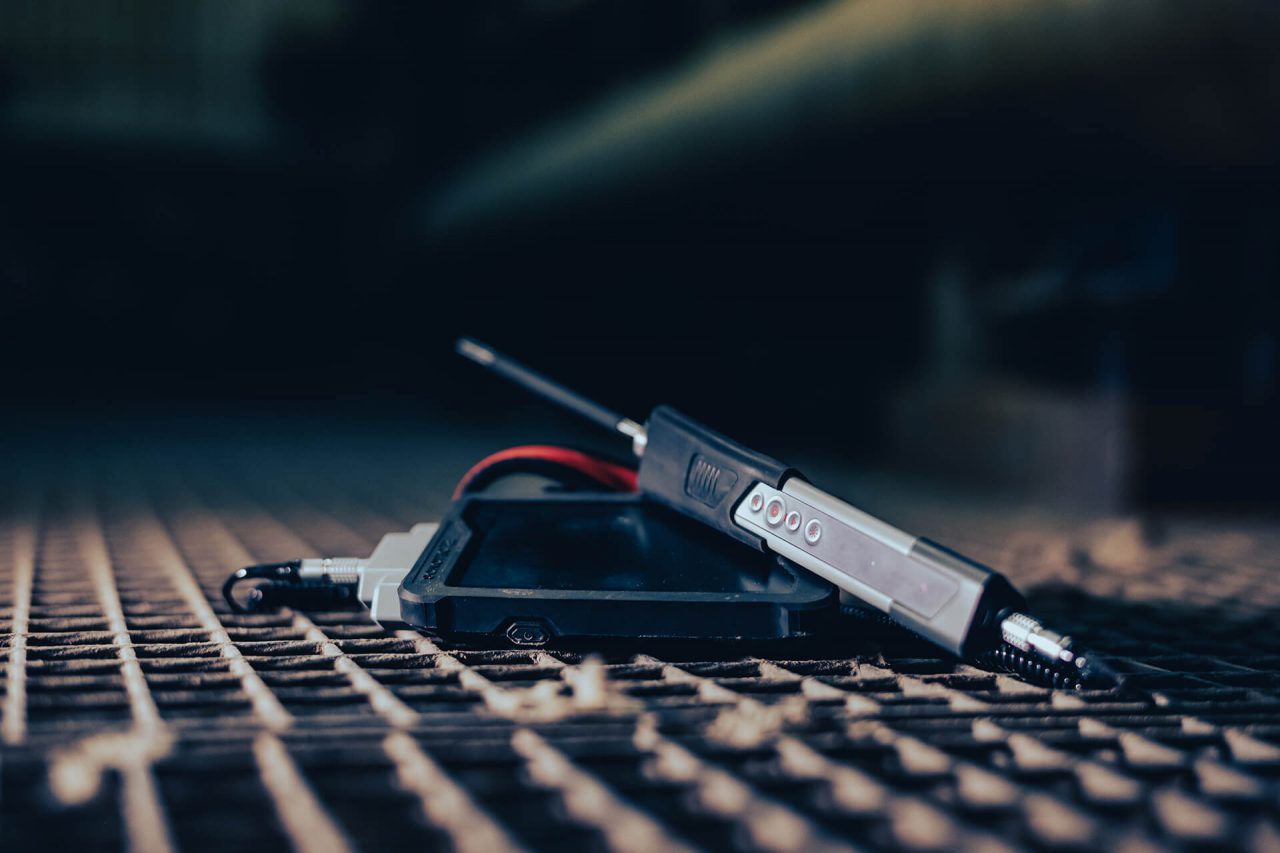
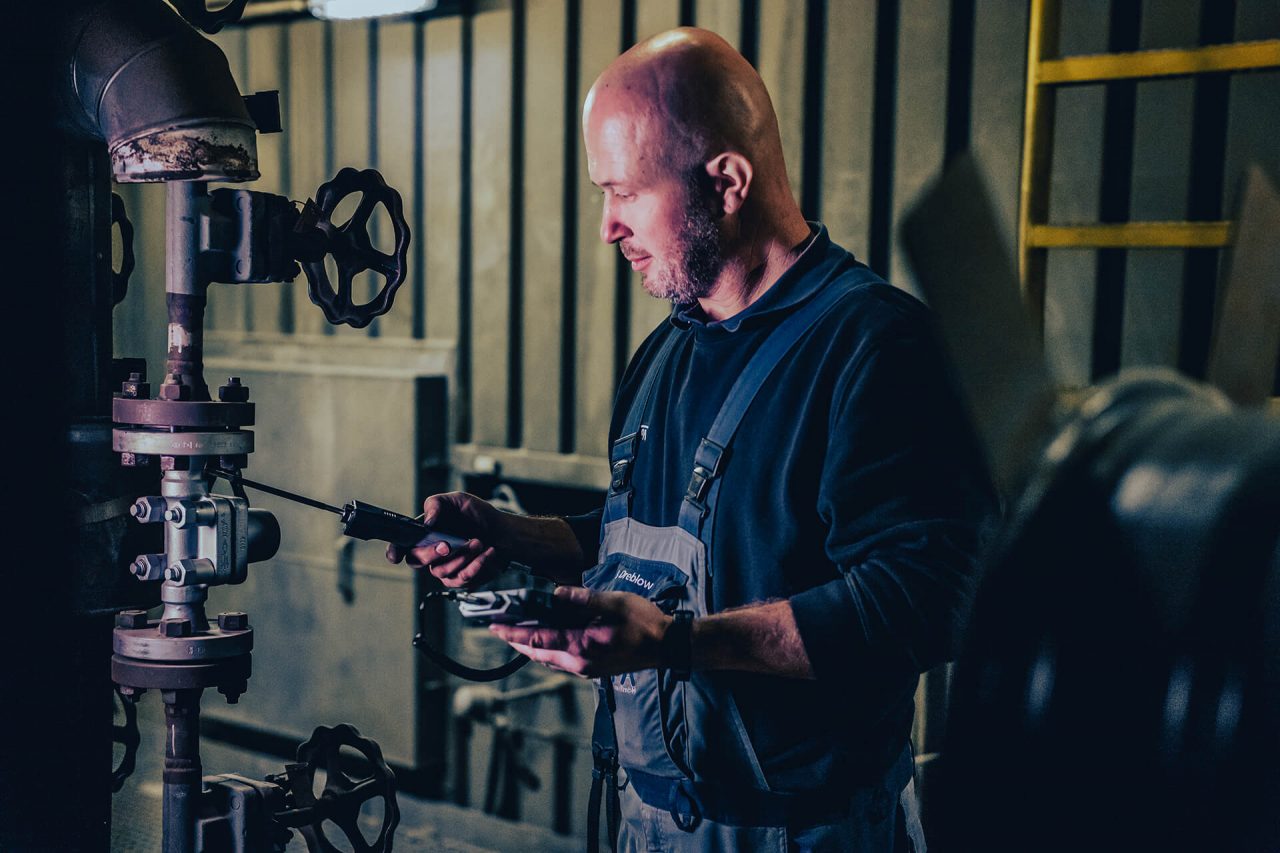
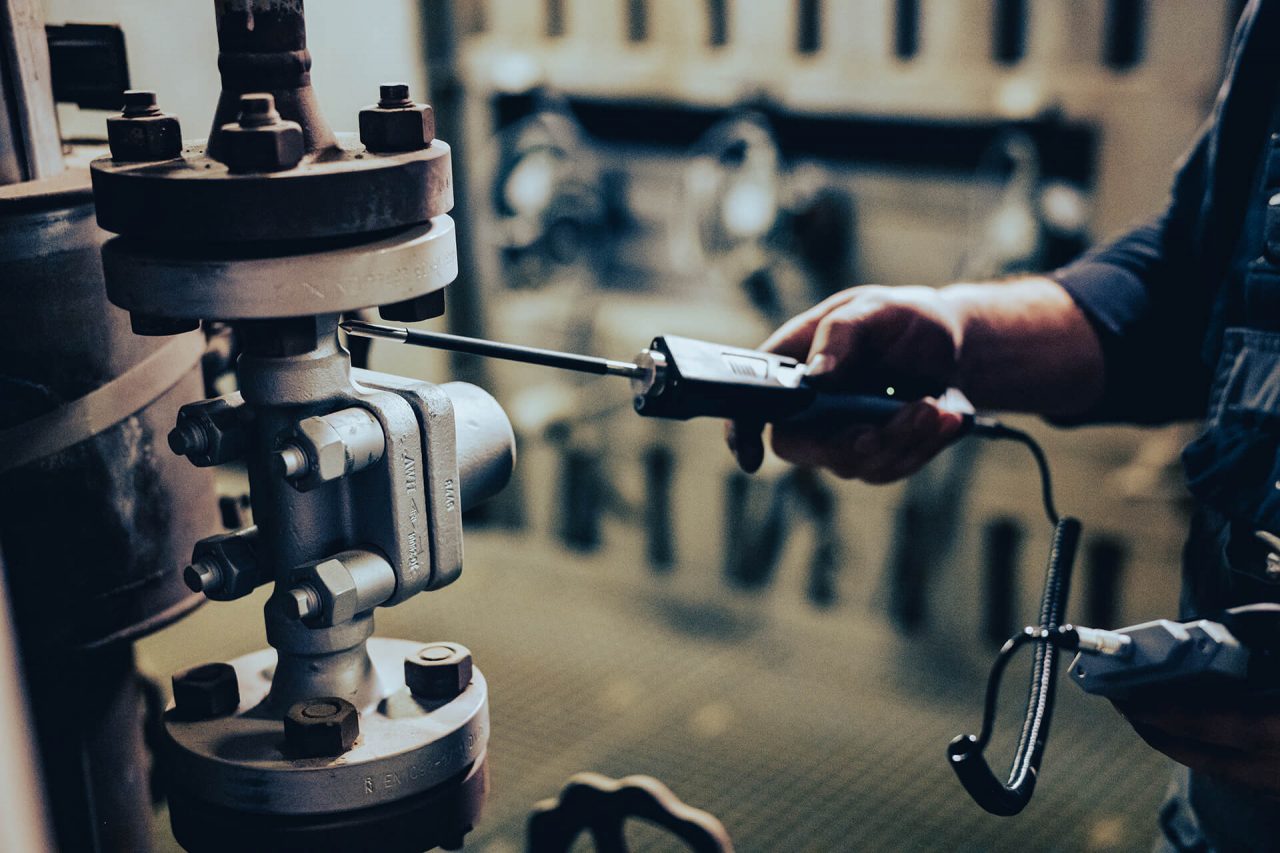